(本网讯) 2021年伊始,作为国内运动品牌龙头企业,安踏集团在其同安工厂打造的智能化、数据化、标准化的一体化工厂正式亮相并投入运营。据悉,该工厂率先在业内实现从裁剪、配料、车缝、整烫、包装、装箱的全品类、全流程贯通式生产,在单品效率提升的同时也让利润率翻倍增长,成为供应链乃至行业可循的标杆。
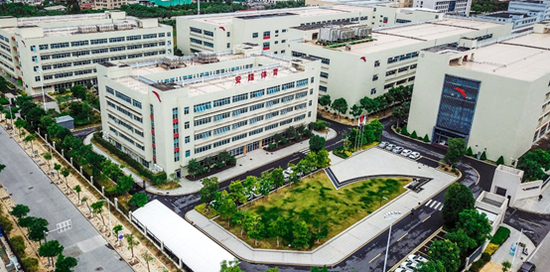
“七大系统”智能改造实现全流程贯通
“我们不做行业一样的。作为行业头部企业,我们有责任为行业创新,率先投入、大胆投入,引领行业发展。”这是在采访中,安踏集团同安服装部生产总监李金胜和他的团队一再强调的。
据悉,与近年来众多纺织服装企业普遍上马的吊挂系统不一样,安踏同安工厂率先实现全流程贯通,已完成了数据采集、AGV传输、集中挂片枢纽、智能柔性吊挂、高速分拣、高速传输和智能包装分拣七大系统的智能改造。
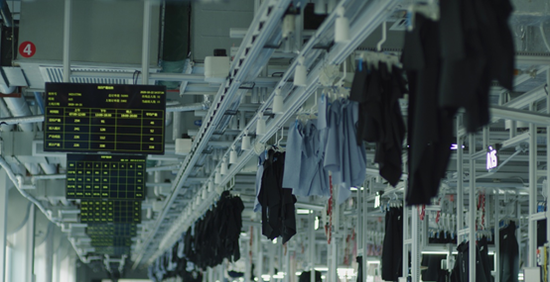
“前端布片上轨道吊挂,一直到成品、打包、封箱,实现全流程自动化。”李金胜介绍,吊挂系统带来了最直观的效率提升,所以不少企业有驱动力改造。但是,前端的物料上吊挂、后端的高速分拣、传输、智能包装等板块,不少企业并未实现全流程贯通。
事实上,系统引进过程中,安踏与供应商系统共进,以产品经理的身份介入硬件生产阶段,探索最适合同安工厂现状和需求的改造安装,实现了跨楼层全品类全流程贯通。贯通的意义,并不在于硬件技术有多先进,而在于对后续整体流程的顺畅,以及未来供应链生产环节与前端消费者数据的进一步对接、升级的空间。
架起“高铁式”路网满足全品类生产
记者站在跨越3层楼的空中流水线下,惊叹于安踏同安工厂流转的产品之丰富。不同品类、不同款式、不同颜色、不同码数的服装都在同一条流水线上生产,这样的场景在整个行业,都是难得一见的。

安踏集团同安工厂的负责人作了个比喻——构成整个体系的智能悬挂系统犹如一张纵横交错的空中高铁路网,每一件衣服都是一名乘客,每一个工位、每一道工序都是一个站点,将整个工厂串联成一条巨大的、错综复杂的流水线网络。
在这里,每一件衣服在裁布阶段就被赋予了自己独特的ID,系统将根据款式、颜色、码数等参数,为它裁剪、匹配好布料,吊挂上生产线,并按照一定频率,送到指定工位,让员工无需取下,就可以完成自己负责的工序,接着自动向下一个站点移动。
在这个系统里,最多可以涵盖多少服装品类?安踏同安智能工厂智能悬挂系统给出的数据是多达500种以上。再加上“七大系统”的全模块串联,智能悬挂系统上线后。以前做一件衣服,周期至少要半个月,现在3个小时就能做出来。
“特别是在我们行业的梭织品类,这条路是很少能走成功的。”生产部统筹经理叶桃绿坦言,梭织的工艺、材料都更加复杂。比如雨翼膜,一撕就破,手势和吊片都十分讲究。以他们之前生产的一款女款长羽绒服为例,单车缝工序就多达108道。叶桃绿表示,他们将更有能力和技术,承接多品牌等精品订单,为整个集团赋能。
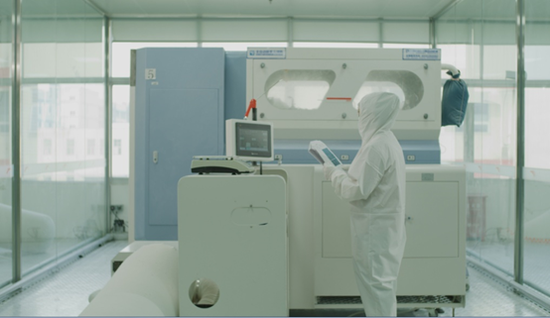
“C位”出道,人机协同实现价值最大化
事实上,智能化升级后,工厂员工的技能也成为数据库中至关重要的一环,包括擅长模块和熟练程度。系统能根据各组别的能力,让最适合的衣服流转到最适合的工作组,甚至可以将三个组中最艰难的工序自动分配给能力最强、技能最优秀的员工,由他占据C位,带动整条生产线品质的提升。
智能悬挂系统实现的,不仅是生产线的平衡,而且是整个工厂的全流程平衡,最大限度地避免了资源浪费,让员工到最需要他的岗位上去,创造更多价值。当流水线上每个员工都被纳入数据智能化的范畴时,推动了人机协同价值最大化。
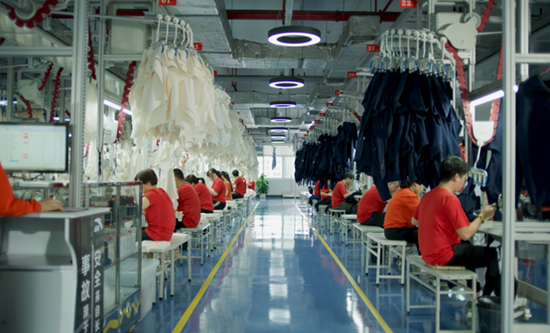
“我们在工作中,人和机器之间不再是相互替代的关系。”车间负责人表示,智能化改造在实现人机互联的基础上,将人的智慧和工作经验嵌入机器的运转当中,与机器精准、高效、灵活等优势有机结合。“在激发工作潜力的同时,赋予机器更高的智慧,产生新的生产力和创造力。”
从技术人员到数据分析人员的转变,对人提出了极高的要求,在升级的过程中,同安工业园孵化了大量具备大数据思维的人才,助推智能化升级改造的进程。“通过这轮的升级,我们的管理团队人员精简了三分之一。重点是,我们的组织架构也同步得到了升级,以应对当前生产方式的改变。”李金胜认为。
查看评论(0)网友评论
发 表 登录|注册